A Fast Track Screed: MasterTop 518
Advantages over conventional "sand and cement" screeds
Want a screed that is fast, economical and with reliable good performance? Impossible?
Master Builders Solutions from BASF has developed a fast setting, pre-bagged cementitious binder to be site mixed with approved aggregates, for a proprietary screed mortar: MasterTop 518.
What is a screed?
The use of screed is very common in residential, commercial and industrial building. A screed is a layer of well compacted material, commonly a mixture of cement, aggregate and water, that is mixed on site and applied on top of a slab base to achieve surface levelness and flatness suitable for receiving a floor finish or to raise the finished floor level to desired elevations.
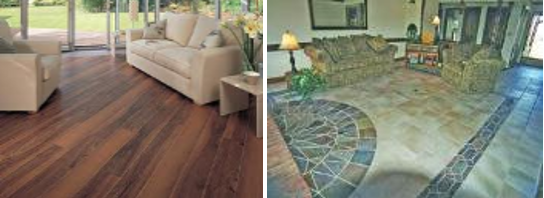
Sand & cement screeds are laid in one of the following forms:
Bonded screeds are applied to hardened floors and act integrally with the base slab. A bonding slurry with good bond strength should be used (MasterTop 500). All the forces acting on the screed are transferred to the base slab through this bond. Good bond strength is also critical to avoid cracking due to internal drying forces, especially around the screed edges.
As per BS 8204-1, bonded "normal sand & cement screed" thickness should not be less than 25 mm or more than 40 mm. MasterTop 518, however, can be laid as thin as 10 mm thickness.
If more than 40 mm thickness is needed, un-bonded screed should be used, as with increased thickness there will be an increasing risk of loss of adhesion to the base due to differential shrinkage stresses.
Unbonded screeds are used either to install a damp proof membrane between the base slab and the screed; when it is impossible to ensure a good bond between base slab and screed (e.g. due to contaminated base slab surface); or when more than 40 mm thickness is required.
In this case the screed is separated from the floor by an impervious layer, such as a polyethylene slip membrane. Un-bonded screeds need to be thicker, in order to resist the forces that cannot be transmitted to the base slab and to resist edge curling.
As per BS 8204-1, unbonded "normal sand & cement screed" thickness should be at least 50mm, whereas MasterTop 518 can be laid in minimum 40mm and up to 160mm thickness.
Floating screeds are laid on heavy duty thermal insulation boards or on sound insulation quilts. As the insulation materials are compressible, the screeds must be thicker and distribute any loads they encounter over as wide an area as possible, to avoid damage to insulation and cracking of screed.
As per BS 8204-1, Floating "normal sand & cement screed" thickness should be at least 75mm, whereas MasterTop 518 can be laid in minimum 40mm and up to 160 mm thickness.
For detailed application procedure, please contact Your Master Builders Solutions representative.
Our offer, Our Promise: Good quality, fast and economical
MasterTop 518 is a proprietary screed system, demonstrating consistently reliable performance that you can depend on in your projects.
MasterTop 518 can be applied down to 10 mm thickness, providing architects with design flexibility.
"Normal sand & cement screed" should be left for 1 day per mm of thickness to cure and dry prior to application of the final floor finish. MasterTop 518 is ready after 3 days! MasterTop 518 is ideal for new built as well as renovation projects.
MasterTop 518 is shrinkage compensated, meaning, compared to "normal sand & cement screed" shrinkage is minimal. Also, all shrinkage takes place in the first 3 days, so floor finish can be laid early without risk of shrinkage cracking and "tenting" in the finished floor.
Compacting a semi-dry screed mix can be challenging. Especially with floating screeds, damaging the insulation underneath is a common problem. MasterTop 518 is mixed to a wet consistency, improving workability of the mix and maximizing compaction of laid screed, leading to a high strength, highly impact resistant screed preventing cracking and failure in the floor finish.
Despite its wetter consistency, 3 days after installation, MasterTop 518 screed has a moisture content of less than 2%, making it possible to lay natural stone without fear of staining or hardwood floor without concern of moisture problems.
MasterTop 518 is part of the BASF Ceramic Tiling and Natural Stone System of Products including adhesive, grout, silicone, waterproofing membrane (for wet areas) that are all compatible with each other and producing a single source supplier system for warranty.
Airport floors, shopping mall floors, station platforms, hotel lobbies etc. require a category A Impact Resistant Floor Screed to prevent cracking and failure of the floor finish. MasterTop 518 passes the BRE Screed Test Hammer for impact resistance after only 3 days, instead of waiting for 28 days.
MasterTop 518 is an economical solution as it saves valuable time during construction. Its main cost advantage though is because of the fact that it can be mixed at 1:6, 1:7, 1:8 binder:aggregate ratios, based on the use and strength requirements.
We welcome your feedback and comments on MasterTop 518. Please do not hesitate to contact us
Stay Connected..