Reinforcement of sprayed concrete for the Mining Industry in South Africa
Unreinforced sprayed concrete, like unreinforced concrete, is a brittle material that experiences cracking and displacement when subjected to tensile stresses or strains. Most of the cracks in concrete are due to the inherent tensile weakness of the material.
Sprayed concrete linings are generally reinforced to absorb tensile stresses, which arise from bending moments in the lining, and to avoid cracking, as well as to provide safety for underground personnel during the works. Reinforcement of sprayed concrete linings may be achieved by means of welded wire fabric (mesh), reinforcing bars (including lattice girders or steel sets) and/or fibers.
For permanent sprayed concrete linings, reinforcement is also installed to avoid the development of cracks in the concrete due to shrinkage, as concrete shrinks and is restrained at the same time, as well as to mitigate temperature stresses.
Steel reinforcement
Steel reinforcement increases the flexural strength of concrete and controls cracks. It is required in installations where structural loads are acting on the concrete lining. As a structural material in sprayed concrete, reinforcement is designed using the same criteria that apply to conventional concrete. It is generally in the form of mesh and it is recommended for thick layers (≥ 50 mm). Usually, a reinforcing mesh of 50 to 150 mm with a wire diameter of no more than 10 mm is widely accepted. Reinforcing bars are seldom used in sprayed concrete sections with a thickness of less than 40 mm.
Mesh reinforcement limits the development and depth of cracks. If properly anchored, mesh reinforcement prevents or retards future peeling of the sprayed concrete layer (debonding), which may result from a poor or non-uniform bond, deterioration of the substrate or overload, among other influences. Proper placement against a structurally sound substrate and an appropriate design avoid debonding of the sprayed concrete at the interface with the substrate.
Small reinforcing bars combined with mesh are used in zones where mesh alone would not be structurally sufficient for the application, e.g. in curved and irregular surfaces, where uniform spacing and cover are critical. The number of layers of mesh required for thicker sections can be reduced by a suitably designed combination of bars and mesh.
The use of lattice girders (arches) allows the control of the excavation profile. They also provide support for spiling (if required), ensure correct positioning and properly secure the mesh reinforcement before the sprayed concrete is applied, additionally providing an initial safeguard against rock falling out of the crown. Lattice girders are available in high yield steel, in preformed configurations of three or four main bars. Separation of the lattice girder in pieces is necessary to suit the different stages of excavation and support. The pieces are bolted together or lapped to form the whole arch after complete excavation. Design requirements will determine whether installation of a continuous lattice arch covering the whole excavation section is required.
The soundest sprayed concrete is generally obtained when the design and position of reinforcement allow the least interference with concrete placement. Hence, small bar sizes are recommended. In any case, the spacing, arrangement and sizing of reinforcement should be done properly, in order to facilitate the placement of concrete and minimize the development of sand pockets and voids. The minimum cover over reinforcement should be according to the job specification or applicable building codes, taking into account environmental influences.
Preformed rolled steel joist or beam sections are sometimes used instead of lattice girders. In this instance, additional care on the part of the sprayed concrete nozzleman is required to ensure proper compaction of the sprayed concrete all around these sections and to avoid the ‘shadow’ effect.
Fiber reinforcement
Fiber-Reinforced Sprayed Concrete (FRSC) is conventional sprayed concrete containing discontinuous discrete fibers. It has been used successfully for ground support for more than 20 years. Typical applications for FRSC are for mine and tunnel linings, rock slope stabilization, surface coatings on rock and soil, fire protection coatings or other structures that may be subject to high deformations or where crack control is needed.
The use of steel or synthetic fibers in sprayed concrete has increased during the last 20 years. It has been accepted by engineers, owners and contractors around the world. These types of fibers have been developed hand in hand with improved concrete technology and application techniques.
Fibers in the concrete mix at normal addition rates can improve flexural and shear toughness, and resistance to impact. Stainless steel fibers increase thermal shock resistance and resistance to temperature cycling damage and crack development in sprayed concrete. The susceptibility of sprayed concrete to plastic shrinkage cracking can be reduced by the addition of synthetic fibers.
Types and classification of fibers
Fibers made of steel, glass, synthetic polymers and natural materials can be used in sprayed concrete. However, glass fibers should not be used as a permanent material for sprayed concrete linings, since glass will deteriorate/degrade in the alkaline environment of concrete. As a consequence, performance will be lost over time. Carbon fibers are not used mainly due to their high cost. As the most commonly used types of fibers are steel and synthetic polymer fibers, only these types are considered here.
Steel fiber reinforced sprayed concrete was first applied in North America at the beginning of 1971 in experimental work. It has been used throughout the world since 1973. Micropolypropylene fibers were first placed in Europe in 1968. In the mid-1990s, macrosynthetic fibers were developed for sprayed concrete applications and they have been used in mining and slope stabilization projects.
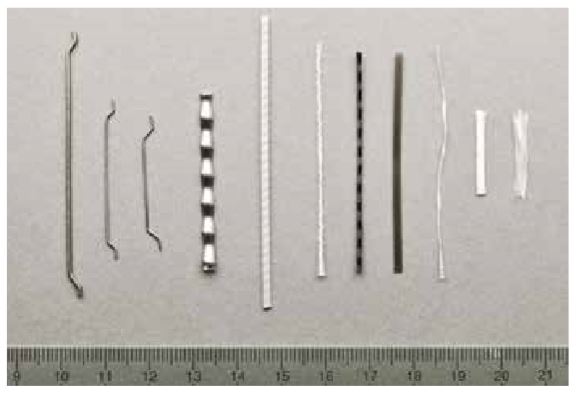
Figure 3-40: Different fiber types. On the left, steel fibers are shown. On the center and right, synthetic fibers are shown.
According to ACI 506.1R-08 [31] fibers for use in sprayed concrete are usually divided into two groups according to their diameter. Fibers with equivalent diameters greater than 0.3 mm are classified as macrofibers, while fibers with diameters of less than or equal to 0.3 mm are known as microfibers. The fineness of microfibers is described by the unit denier. Typical synthetic fibers used in sprayed concrete have a denier of 6, which corresponds to an equivalent diameter of 32 μm (0.0032 mm).
Macrofibers can be characterized by their aspect ratio (the ratio of length to diameter of a fiber). Typical aspect ratios of macrofibers for sprayed concrete vary from 40 to 65 for common fiber lengths (19 to 50 mm). Most of the macrofibers used in sprayed concrete are either steel or synthetic fibers. Steel fibers are generally between 19 to 35 mm in length and have an equivalent diameter between 0.4 and 0.8 mm. The length of synthetic macrofibers can vary from between 40 to 50 mm and their equivalent diameters are similar to those of steel fibers.
Microfibers for use in sprayed concrete are usually polyolefin-based or nylon-based. The length of synthetic microfibers ranges from 6 to 50 mm. Microfibers which are used to resist explosive spalling in fires should be polypropylene-based, with equivalent diameters of less than 33 μm and a length under 12 mm.
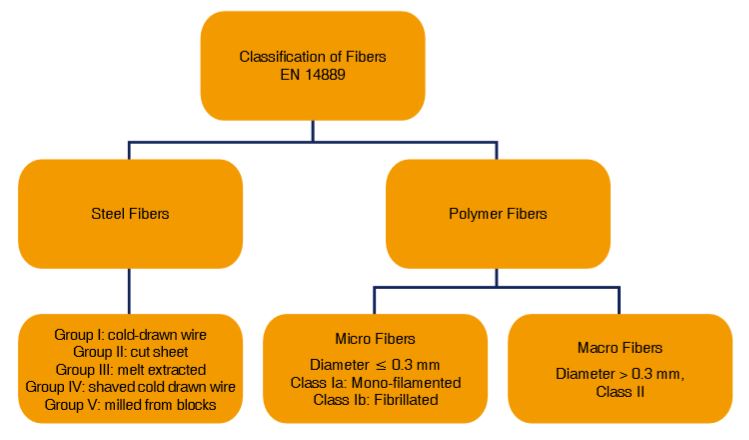
Figure 3-41: Classification of fibers for structural or non-structural use in concrete, mortar and grout, based on EN 14889
The European Standard EN 14889 specifies requirements for steel and polymer fibers for structural and non-structural use in concrete (including sprayed concrete), mortar and grout. Fibers are used for structural purposes where the addition of fibers is designed to contribute to the load-bearing capacity of a concrete structure. According to EN 14889, fibers are classified as shown in Figure 3-41.
According to EN 14889 steel fibers shall be classified into one of the above-mentioned groups, in accordance with the basic material used for the production of the fibers. Polymer fibers used in sprayed concrete are classified by two main classes, generally divided by their diameter. Polymer microfibers (class Ia and Ib) are fibers with a diameter of less than or equal to 0.3 mm. Polymer macrofibers (class II) have a diameter greater than 0.3 mm.